Medical device manufacturing requires line clearance and changeover activities to ensure appropriate traceability and lot segregation to avoid material and product mix-ups. During changeover, there is no product being built, and reducing the amount of time during changeover can have a significant difference in the daily output of a production line. Most engineers ignore changeover because the activities are usually performed by quality personnel and the automation does not appear to be a viable solution for changeover.
We developed a tool to help facilitate quick changeovers for manufacturers that require lot segregation and lot material identification: Electronic Work-in-Process Tags.
Operational Velocity has developed a well-defined methodology using work-in-process tags to replace the manual entry of individual work-in-process tags and lot dividers. Removing paper from manufacturing saves supply expenses associated with paper, ink, and printer maintenance as well as reducing the particulate generated in a clean room. Reducing the time for changeover and eliminating waste can be systematically implemented by using SMED (Single Minute Exchange of Dies) tools. SMED was developed by Shigeo Shingo, a Japanese industrial engineer who helped companies dramatically reduce their changeover times. His pioneering work led to documented reductions in changeover times averaging 94% across a wide range of companies.
SMED Changeover Analysis
Changing from one lot of product to another requires a changeover and can be represented by the following:

The first step in SMED is to break down the changeover activities into ‘internal’ and ‘external’ activities. Internal activities are required to be performed within the start/end lot dividers of the process and external activities can be performed outside of the production line. The following is a representative analysis of the changeover activities and potential streamlining opportunities using paper. Different companies have different practices based on the timing of the data collection of their ERP system, but the following steps are representative of most medical device manufacturers.
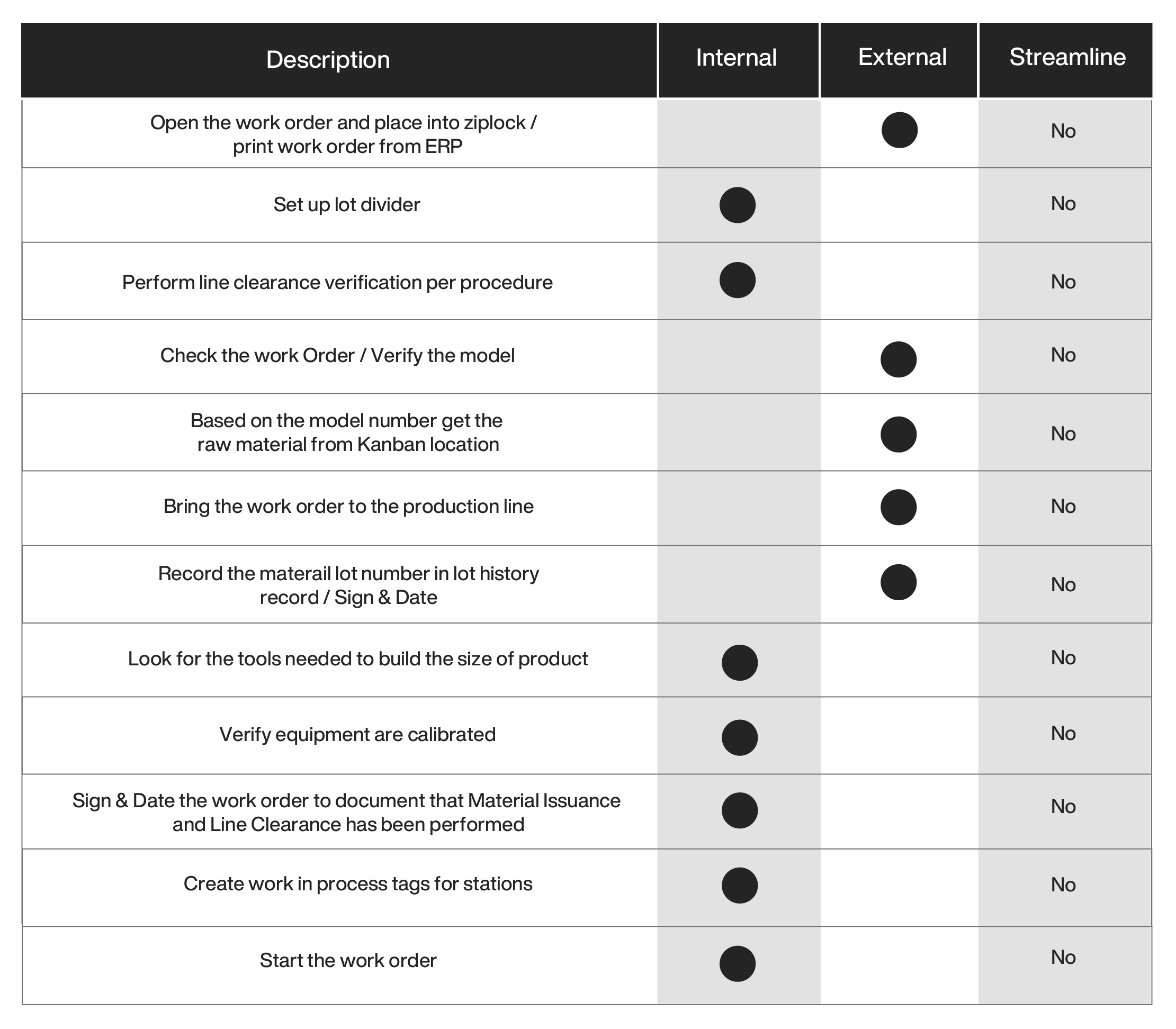
Moving the external activities to be performed by nonessential personnel on the production line (e.g., kitting lots with all the material and documentation offline) can be achieved if there is sufficient space and personnel. Examining the process steps after removing the external steps results in the following:
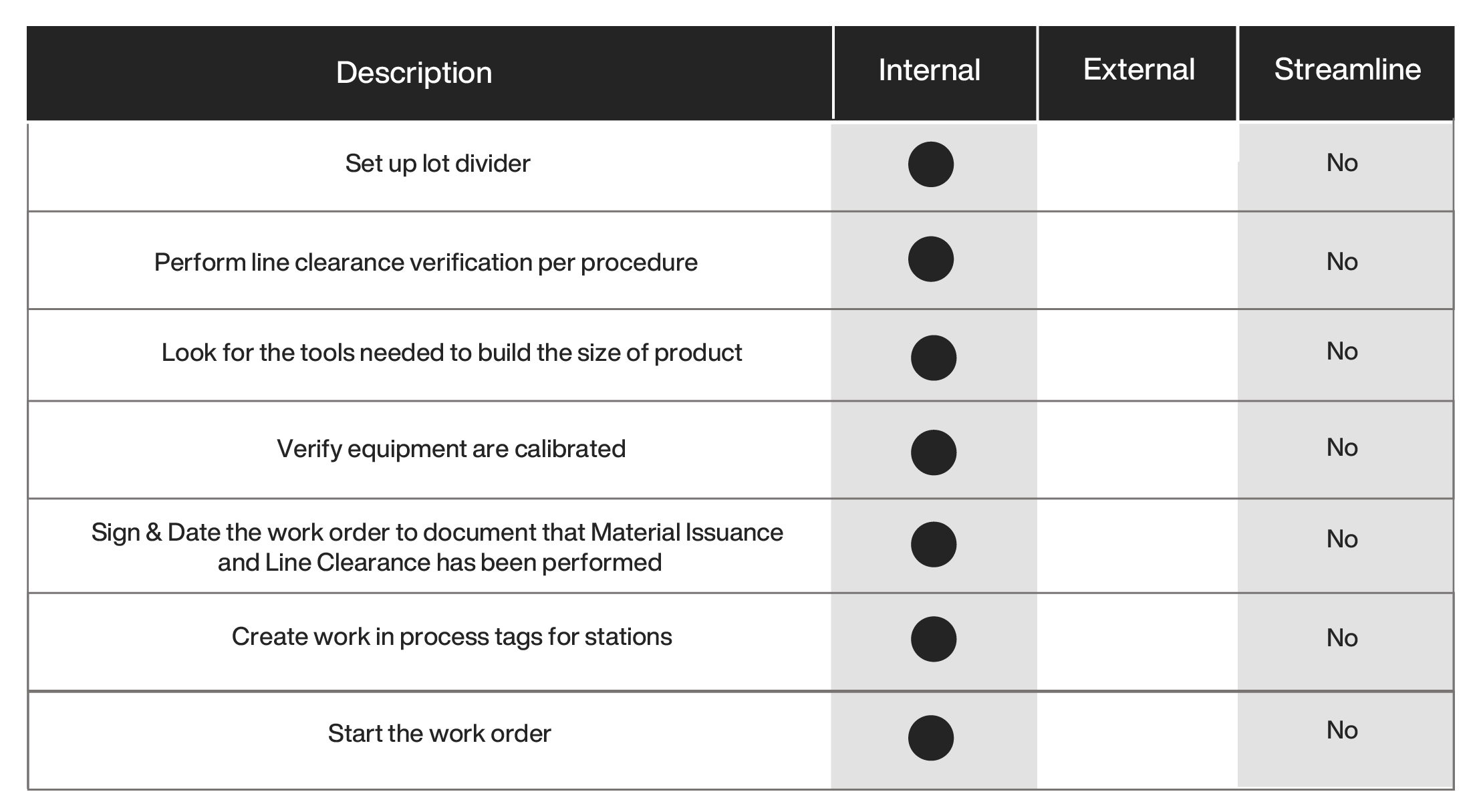
The benefits of electronic work in process tags and dividers are the following:
- The multiple displays can be updated with a single data entry
- Bar codes enable scanning and automated data entry
- Fixed displays remove unnecessary personnel movement to retrieve printed lot information and replace lot dividers
- Using electronic displays for calibration due dates and maintenance due dates also enables scanning and removes manual entry into the lot history record
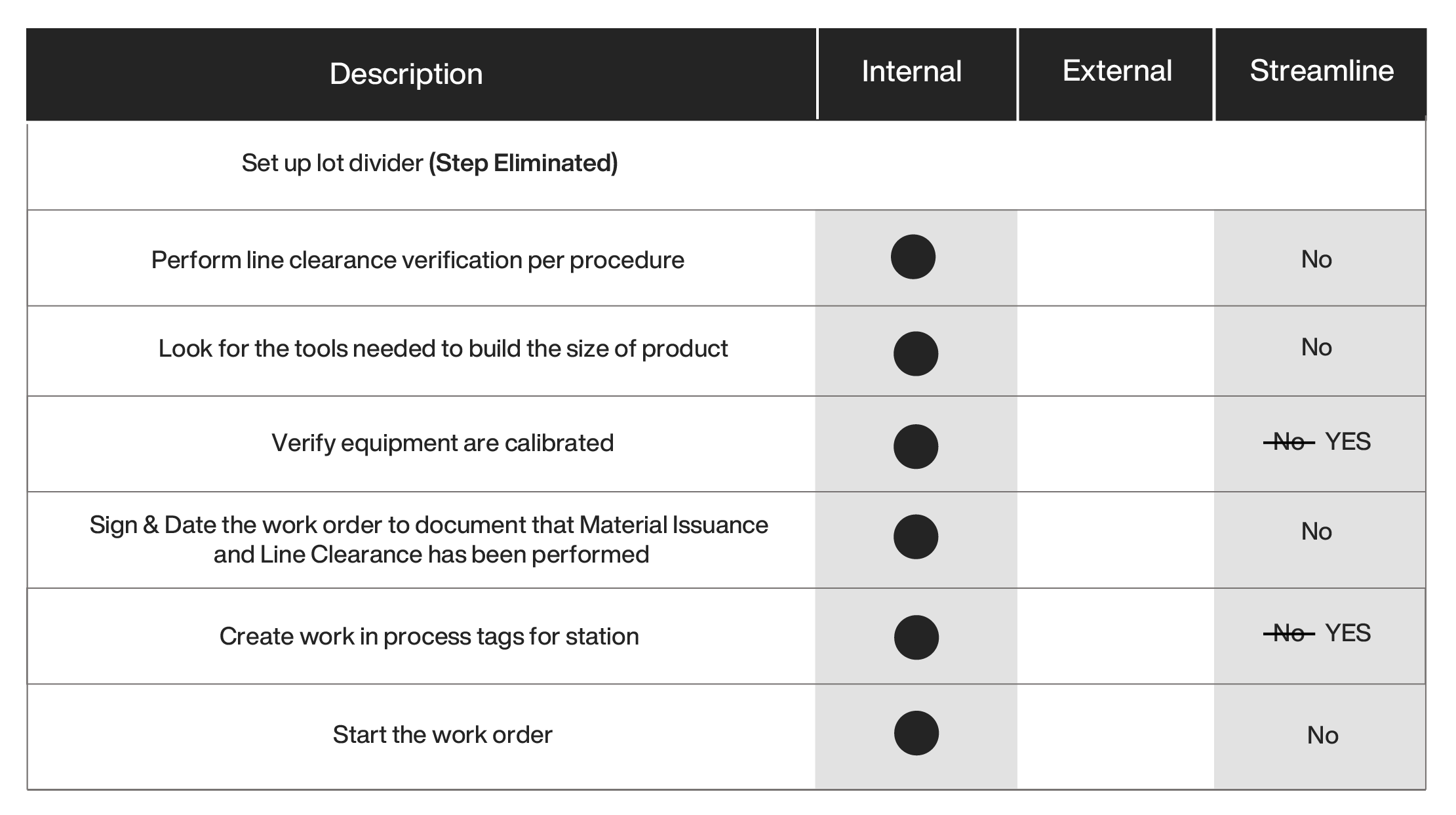
The cumulative impact of performing external activities in parallel, eliminating unnecessary steps, and streamlining the steps using electronic work-in-process displays as a solution for manufacturing changeover can be shown below:
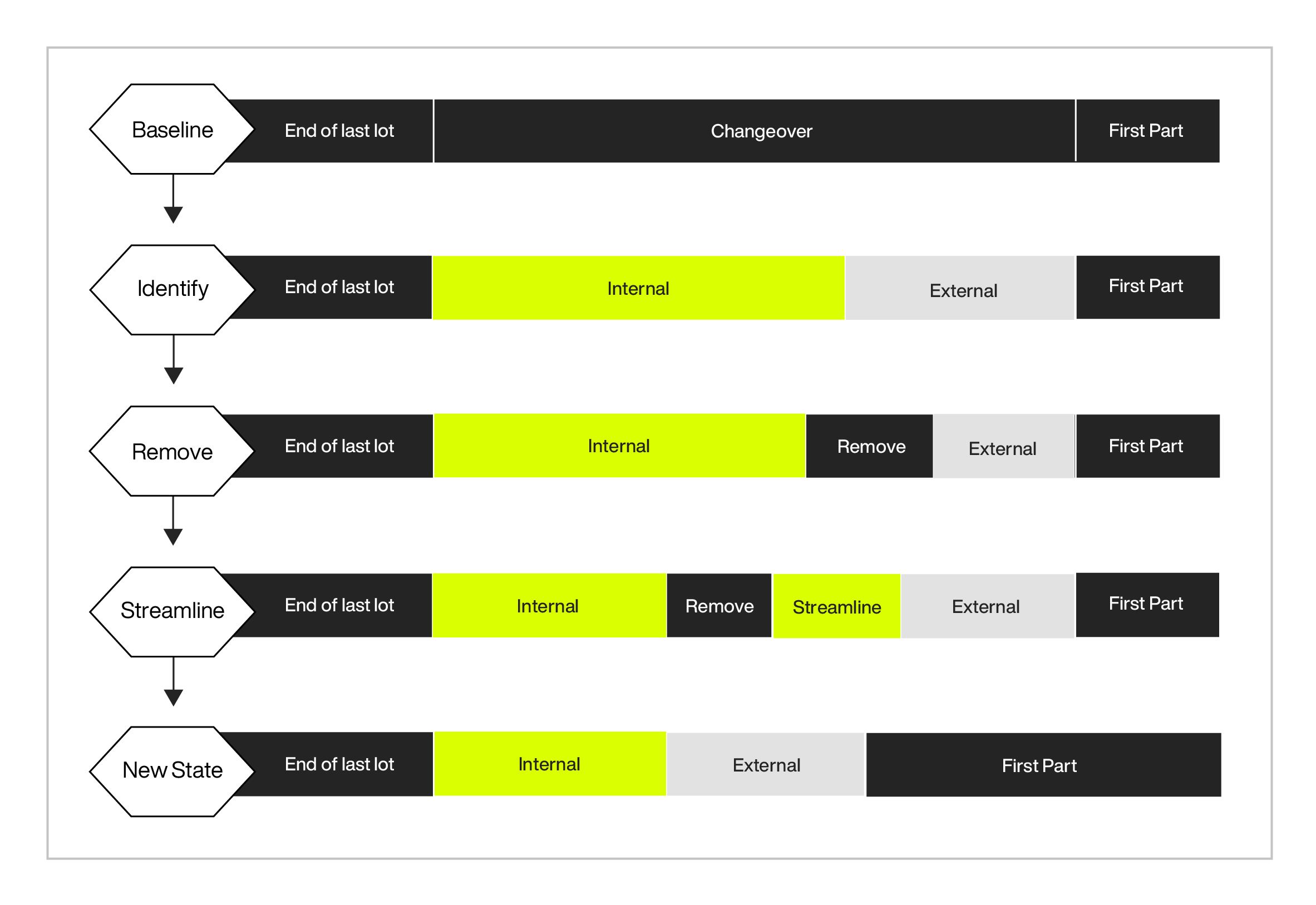
How does a productivity improvement effect product costs?
- Change over time (baseline): 15 min (average)
- New change over time using electronic display: 5 min (average)
- Changeover reduction: 15 min – 5 min = 10min
- Assuming 1 production line / 2 changeover per day: 10 min/changeover x 2 changeover/day x 250 mfg day / 60 minutes/hr = 83.3hr (annually)
- 83.3x ($25/hr fully burdened labor rate + $75 Ovd Rate) = $8,333 / production line
Assuming there is a subassembly line, top assembly, and packaging line, each with separate work orders, the savings is easily 3 x $8,333 = $25,000 per year.
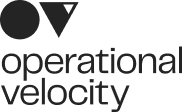
Operational Velocity
109 N Maple St, Unit J
Corona, CA 92878-3298
951 475 7038 | 949 445 0532
© 2024 Operational Velocity